Unleashing the Power of Installed Base Data: Industrility’s Solution to True Total Cost of Ownership
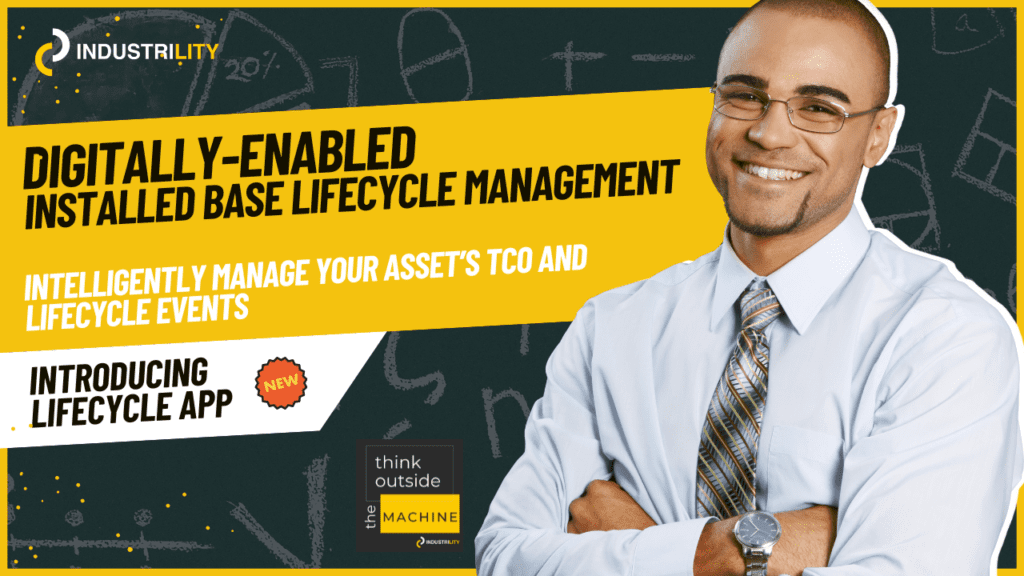
In today’s fast-paced industrial landscape, businesses are constantly seeking ways to optimize their operations and improve efficiency. One critical aspect often overlooked is understanding the true total cost of ownership (TCO) of equipment. TCO goes beyond the initial purchase price, encompassing all costs associated with the entire lifecycle of the equipment. In this blog post, we’ll delve into the significance of TCO, the components it includes, and how Industrility can empower your organization to unlock the installed base data and streamline the management of lifecycle costs.
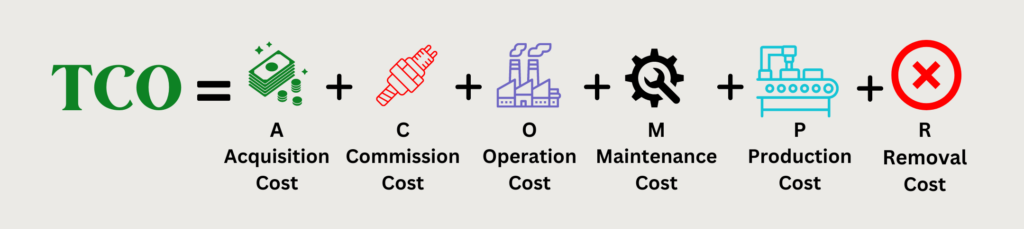
Understanding TCO
TCO is a comprehensive approach to evaluating the financial impact of owning and operating equipment throughout its entire lifespan. While the purchase price is a significant factor, TCO considers various other elements, including:
- Cost of Acquisition (A) includes the cost of engineering, procurement, equipment, auxiliary equipment, inspections, and documentation.
- Cost of Commissioning (C) includes transportation, construction, testing, and training
- Cost of Operation (O) includes energy consumption, in-house crew, facility costs, and handling materials.
- Cost of Maintenance (M) includes maintenance personnel, testing tools, spare parts, and repair costs, sometimes includes upgrades, modernization or remanufacturing
- Cost of Production (P) includes production losses, downtime costs, quality control costs, environmental costs, and redundancy costs.
- Cost of Removal and Disposal (R) includes the cost of removing and disposing of the asset, minus any salvage/recycle value.
Why TCO Matters
Gain unparalleled insights into product performance, enabling proactive measures to enhance reliability and efficiency for ultimate competitive advantage. Similar to “CarFax” reports, Industrility helps Manufacturers can help track the overall condition of the equipment, that includes TCO calculations, historical maintenance records and consumption so it provides visibility and transparency, subsequently boosting its resale value in the secondary market.
Optimizing investments Operational costs, such as energy consumption, routine maintenance, and unexpected repairs, often eclipse the initial purchase price over time. By carefully understanding the CapEx (Capital Expenditure) and OpEx (Operating Expenditure) for each of the above costs provide the visibility of the overall costs.
Understanding Lifecycle Costs (LCC) and its relation to TCO
LCC takes a big-picture view of equipment ownership, considering all the costs associated with it throughout its entire lifespan. While there are various ways to calculate Lifecycle costs (LCC), Industrility has created a model that helps relates LCC to TCO. LCC might involve more detailed cost breakdowns throughout the lifecycle, less the cost of operations such as energy/fuel consumption, while TCO may provide a more general picture of ownership costs.
LCC = TCO – O
Why LCC Matters
- Design more cost-effective equipment: By understanding the full cost of ownership for their products, manufacturers can design equipment that is not only reliable but also easy and affordable to maintain. This can lead to a competitive advantage.
- Marketing well to potential buyers: Equipping salespeople with LCC data allows them to demonstrate the true value proposition of their products. Buyers appreciate a transparent discussion that goes beyond the initial purchase price.
- Develop better service offerings: Understanding the maintenance needs of their equipment allows manufacturers to develop targeted service packages that address customer pain points and generate recurring revenue streams.
- Making informed purchasing decisions: Focusing solely on upfront costs can lead to a false sense of economy. LCC helps identify equipment that offers the best overall value over its lifespan.
- Budgeting more effectively: By understanding the ongoing costs associated with equipment ownership, businesses can better plan for maintenance expenses and avoid unexpected budget shortfalls.
- Optimizing equipment performance: A proactive maintenance approach, informed by LCC data, can extend equipment life, improve efficiency, and reduce downtime.
Introducing the Lifecycle App
To address the above concerns for the manufacturers, so that they can provide the right visibility to their owners and operators, we have built the Lifecycle app. Lifecycle App is one of the several apps in the Industrility’s app platform that helps manufacturers track lifecycle of an asset as well as the overall Installed base using lifecycle events. Industrility’s Data Ingestion Engine, powered by OpenAI LLMs, carefully and intelligently extracts lifecycle related information (cost, timeline, asset serial number, location etc.) from variety of data sources (such as invoices, service technician report, CSRs, spare parts catalog) and hydrates the digital twin of the asset. It collects and connects to various sources to build the installed base map for the manufacturer throughout the various phases and stages of the equipment lifecycle. By curating and categorizing these lifecycle events, the lifecycle app provides detailed visibility of the TCO and LCC cost of each asset over its useful life and overall Installed Base.
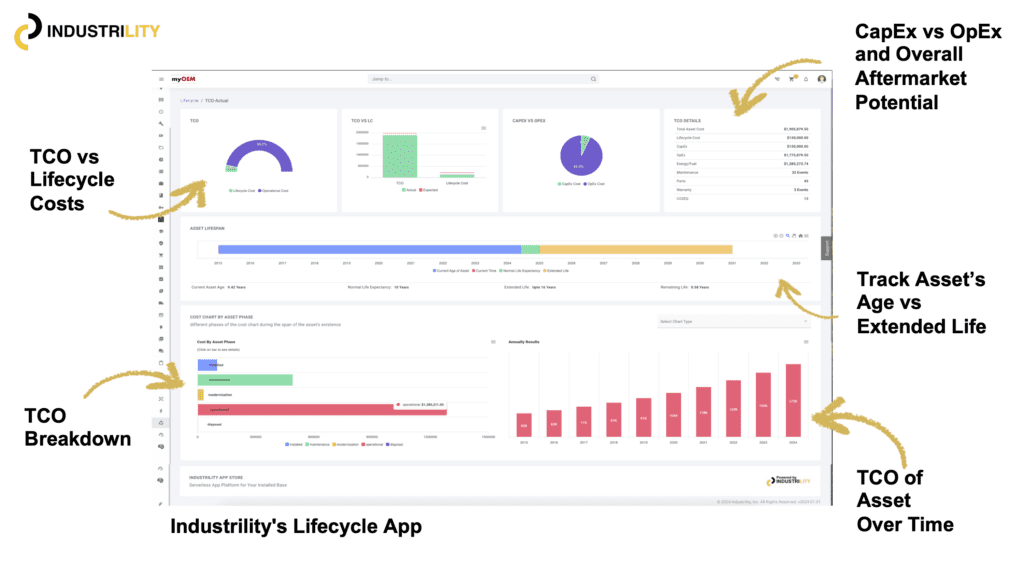
By understanding the intricacies of TCO and LCC, manufacturers and owners alike can make data-driven decisions across each phase and stage. These phases and stages are configured by equipment model, model family and business model (product-only, product-service, product-leased and as-a-service)
The Lifecycle app tracks overall installed base lifecycle (which asset is at what stage and what phase) and Individual asset’s costs throughout its lifecycle, categorizes them into CapEx and OpEx, providing clear view of overall aftermarket potential (or lost aftermarket revenue). Here’s how Lifecycle App can help:
- Centralized Data Management: Industrility aggregates data from various sources, creating a centralized hub for all your equipment information.
- Proactive Maintenance: Anticipate maintenance needs and potential downtime, allowing for proactive decision-making and cost-saving measures.
- Customized Reporting: Generate detailed TCO reports tailored to your business needs, facilitating transparent communication and strategic planning.
- Lifecycle Tracking: Industrility tracks the entire lifecycle of your equipment, ensuring you have a comprehensive understanding of its costs from acquisition to disposal.
This unlocks a range of new possibilities:
- AI-powered Design Optimization: Industrility GenAI Platform can analyze vast amounts of data on existing equipment performance, user feedback, and maintenance needs. This allows it to generate innovative equipment designs that not only perform well but are also easier and cheaper to maintain throughout their life cycle.
- Predictive Maintenance Recommendations: The Platform can analyze sensor data from equipment in real-time, predicting potential failures before they occur. This empowers manufacturers to recommend preventative maintenance schedules to owners, extending equipment lifespan and reducing overall maintenance costs.
- Data-driven Service Package Creation: The Platform can analyze LCC data to identify common maintenance pain points for specific equipment types. This allows manufacturers to develop targeted service packages that address these issues, increasing customer satisfaction and creating new revenue streams.
- AI-powered LCC Analysis: The Platform can analyze equipment specifications, historical data, and industry benchmarks to create a customized LCC analysis for specific equipment model, model family or business model. This empowers owners to make informed purchasing decisions based on long-term value, not just upfront cost.
- Dynamic Maintenance Scheduling: AI can analyze real-time equipment data and integrate with maintenance scheduling software. This allows for dynamic adjustments to maintenance schedules, optimizing resource allocation and minimizing downtime.
- AI-assisted Part Procurement: Generative AI can analyze historical maintenance data and predict future parts needs. This allows owners to automate parts procurement, ensuring they have the right parts on hand when needed, reducing downtime and improving operational efficiency.
Conclusion
In the competitive landscape of the industrial sector, unlocking the installed base data and understanding the true total cost of ownership is a game-changer. Industrility empowers businesses to make informed decisions, optimize operations, and ultimately enhance their bottom line. Embrace the future of equipment management with Industrility and take control of your TCO and LCC today.
— Jinesh