Making Effective Digital Twins a Reality for Your Industrial IoT Strategy
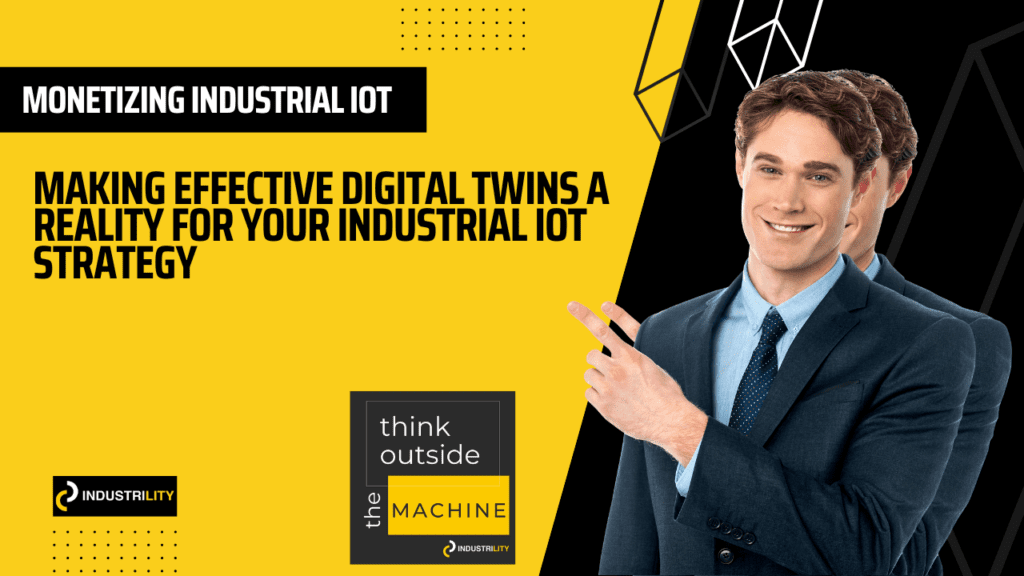
A digital twin is a dynamic, virtual replica of a physical asset, system, or process that is continuously updated with real-time data. In the context of IIoT (Industrial Internet of Things), digital twins enable manufacturers to monitor, analyze, and optimize their machinery and operations.Â
By creating a digital counterpart to your physical assets, you can simulate different scenarios, predict potential issues, and make data-driven decisions that improve efficiency and reduce costs. Enhancing this digital-twin with other information like Parts bill-of-materials, training, maintenance, service, reporting and analytics generates an operational digital twin (Soul) which stays alive throughout the lifetime of the machinery (Body).Â
How Complex Is Digital Twins Technology? How Does My Bottom Line Grow?Â
Implementing digital twins as part of your IIoT strategy offers numerous benefits, including:Â
- Enhanced Predictive Maintenance: Digital twins allow you to monitor the health of your machines in real-time, predicting potential failures before they occur. This proactive approach reduces downtime and maintenance costs while extending the lifespan of your equipment.
- Optimized Operations: By simulating different operating conditions and scenarios, digital twins help identify bottlenecks and inefficiencies in your processes. This enables you to make adjustments that improve productivity and reduce waste.
- Improved Product Development: Digital twins provide valuable insights into how your machines perform in real-world conditions. This data can inform product development, leading to more robust and reliable machinery.
- Increased Aftermarket Revenue: With detailed knowledge of your installed base and machine performance, you can offer targeted aftermarket services such as maintenance packages, spare parts, and upgrades. This not only enhances customer satisfaction but also generates additional revenue streams.
- Data-Driven Decision Making: Digital twins consolidate data from various sources, providing a comprehensive view of your operations. This enables you to make informed decisions based on accurate and up-to-date information. Â
Industrilty’s after-sales strategy
Industrility’s app platform helps monetize industrial IoT primarily through its SaaS platform tailored for heavy machinery manufacturers and OEMs. We help OEMs shift from reactive to proactive maintenance, reducing downtime for their customers and creating new revenue streams through service contracts.
Â
Are you struggling to Monetize IIoT?
Â
Here are some strategies:Â
 Linking IoT to Parts Recommendation and Parts SaleÂ
The integration of IoT in machine manufacturing significantly enhances parts recommendation and parts sales. IoT sensors on machines provide real-time data on parts’ conditions and usage patterns. By analyzing this data, digital twins can predict when a part is likely to fail or requires replacement. This proactive approach not only minimizes downtime but also streamlines the parts procurement process. With accurate recommendations, manufacturers can ensure that the right parts are available when needed, boosting genuine parts sales and improving customer satisfaction.Â
 Â
 Creating Servitization Business Models Powered by IoTÂ
 Servitization involves transforming from a product-centric to a service-centric business model. By leveraging IoT, manufacturers can offer advanced services such as uptime services, performance guarantee or even equipment-as-a-service. These services drive higher profitability by reducing operational costs and increasing equipment uptime. The ability to offer value-added services justifies IoT investments, as it opens new revenue streams and strengthens customer relationships. Industrility’s platform enables manufacturers to easily create and manage these servitization models, driving long-term profitability.Â
 Â
 Using IoT to Drive SustainabilityÂ
 IoT plays a crucial role in driving sustainability by extending equipment lifetime and enabling predictive maintenance. Continuous monitoring of machine conditions helps identify potential issues early, preventing major breakdowns and reducing waste. Additionally, IoT data allows for more efficient use of resources, such as optimizing energy consumption and minimizing emissions.  Â
Â
 Using IoT to Provide Advanced Analytics for End OwnersÂ
 For end owners, IoT-driven advanced analytics provide valuable insights into machine performance and operational efficiency. By collecting and analyzing data from various sources, digital twins offer a comprehensive view of the equipment’s health and productivity. This information empowers owners to make informed decisions, optimize processes, and enhance overall performance. With Industrility’s GenAI-powered platform, end owners can get actionable insights, ensuring their operations run smoothly and efficiently.Â
 Â
What Kind of Investment Should I Expect to Make?Â
 To successfully implement digital twins in your IIoT strategy, follow these steps:Â
- Define Clear Objectives: Identify specific goals you want to achieve with digital twins, such as improving maintenance practices, optimizing production processes, or enhancing product development. Clear objectives guide your implementation and help measure success.
- Invest in the Right Technology: Digital twins rely on sensors, IoT devices, data analytics, and artificial intelligence. Invest in robust and scalable solutions that can handle your operations’ data volume and complexity. At Industrility, our GenAI-powered platform provides the necessary tools to create and manage digital twins effectively.
- Collect Comprehensive Data: Ensure your machines are equipped with sensors and IoT devices that collect real-time data on performance, usage, and environmental conditions. Integrate this data into a central platform for analysis and visualization.
- Develop Accurate Models: Create accurate models of your physical assets that reflect real-world characteristics and behaviors. Use historical data and expert knowledge to build detailed simulations predicting future performance and identifying potential issues.
- Leverage Advanced Analytics: Use advanced analytics and machine learning algorithms to extract valuable insights from digital twins’ data. These tools identify patterns, predict outcomes, and optimize At Industrility, our GenAI capabilities enhance digital twins’ analytical power, providing deeper insights and more accurate predictions.
- Measure and Iterate: Regularly assess digital twin implementation performance against predefined objectives. Use key performance indicators (KPIs) to measure success and identify areas for improvement. Continuously iterate and refine digital twin models and processes to enhance their effectiveness over time.
Â
To illustrate the impact of digital twins and IIoT, consider these real-world applications:Â
 Â
1. Predictive Maintenance in Heavy Machinery: A leading construction equipment manufacturer used digital twins to monitor fleet health. By analyzing real-time data on machine usage and environmental conditions, they predicted component failures and scheduled proactive maintenance. This approach reduced downtime by 30% and extended equipment lifespan by 20%.Â
 Â
2. Optimizing Production in Smart Factories: A large automotive manufacturer used digital twins to simulate and optimize production processes. By modeling different scenarios and analyzing IoT sensor data, they identified bottlenecks and optimized workflows. This resulted in a 15% increase in productivity and a 10% reduction in production costs.Â
Â
3. Enhancing Product Development for Industrial Equipment: An industrial equipment manufacturer leveraged digital twins to test and validate new product designs. By simulating real-world operating conditions, they identified potential issues and made improvements before building physical prototypes. This accelerated the product development cycle and resulted in more reliable and robust machinery.Â
 Â
Our platform uses IoT to enhance sustainability through extended equipment lifetimes and predictive maintenance. Additionally, advanced analytics empower end owners to optimize operations. Investing in IoT is crucial for OEMs to stay competitive, as it maximizes efficiency, reduces downtime, and opens new revenue streams, ensuring long-term success in a rapidly evolving market.Â
ConclusionÂ
Â
Digital twins represent a powerful tool for transforming your industrial operations and unlocking new levels of efficiency and profitability. At Industrility, we are committed to helping machine manufacturers harness digital twins’ full potential as part of their IIoT strategy. By following the steps outlined in this article and leveraging our GenAI-powered platform, you can create effective digital twins that drive innovation, optimize performance, and generate significant business value.Â
Â
As you embark on this journey, remember that digital twins are not a one-time implementation but a continuous process of improvement and refinement. With the right technology, data, and expertise, you can make digital twins a reality for your industrial IoT strategy and position your business for long-term success.Â