The Dreaded Job Folder: The Manufacturer’s Real Villain
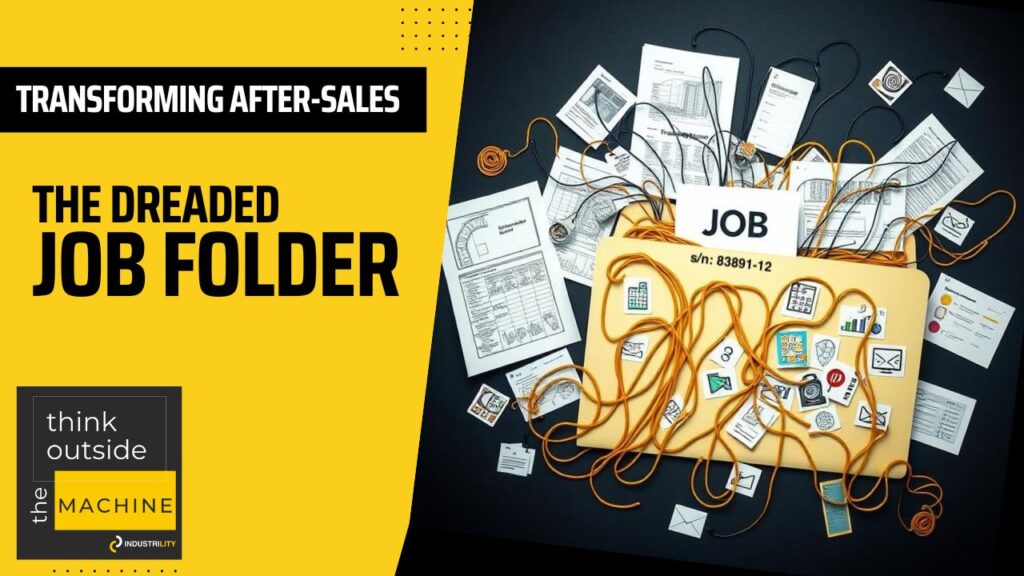
In the world of manufacturing, few things are more infamous than the “Job Folder.” This chaotic digital repository is a bane for many companies, filled with a hodgepodge of documents and data related to equipment sold in the field. From Excel sheets and PDFs to engineering drawings, commissioning documents, and sales orders, the Job Folder becomes a labyrinth of nested directories. Navigating this digital jungle is not only time-consuming but also mentally exhausting, making it a significant pain point for employees and executives alike.
The Problems
The Unorganized Reality
Manufacturers often rely on vast Shared Network drives or OneDrive folders to store crucial machine data. These folders are meant to represent a comprehensive collection of documents for each piece of equipment sold. However, the reality is far from ideal. The data is scattered, referenced to black hole, inconsistently labeled, and poorly organized. Here’s a glimpse into the chaos:
- Multiple File Formats: Excel sheets, PDFs, engineering drawings, and commissioning documents are all jumbled together.
- Version Control Issues: Various versions and revisions of the same document coexist, making it difficult to identify the most recent or accurate information.
- Nested Folders: Deeply nested directories make navigation a nightmare, often leading to dead ends or duplicated efforts.
- No User Tracking: As employees move on, applying best practices are discontinued. This results in no traceability.
- Inconsistent Standards: As ERP systems evolve and new standards are half-adopted, the organization of these folders becomes even more erratic.
The Time-Consuming Search
For a new hire, the Job Folder is a baptism by fire. Finding a specific document or piece of information can take hours, if not days. The lack of a structured approach to data storage means employees must sift through countless files, often relying on guesswork and institutional knowledge. This inefficiency isn’t just frustrating—it directly impacts productivity and morale. People with the “tribal knowledge” often withhold information or are not available when we need them, resulting in even more time consumption. A typical response to a RFQ is supposed to take 1 hour, is delayed to 5 days, resulting in lack of sale because often the first to quote wins!
Massive Lost Opportunities
Beyond the immediate frustration of finding documents, the disorganized Job Folder poses a significant barrier to data analysis. With information scattered and inconsistently labeled, compiling a comprehensive view of the installed base is nearly impossible. This lack of a “Full Installed Base View” means:
- Inefficiencies Go Unnoticed: Without a clear picture of all equipment and its associated data, identifying and addressing inefficiencies is challenging.
- Decision-Making is Hindered: Executives struggle to make informed decisions when they can’t easily access or analyze critical data.
- Missed Aftersales Opportunities: Potential insights that could drive improvements and proactive reminders are lost in the noise.
Never-ending ERP Migrations
ERP migrations are meant to streamline operations and improve data management. However, as these migrations occur across employee generations, they often exacerbate the problem. New standards are only partially implemented, and old habits persist, leading to even greater inconsistency and version hell in this “Job Folder”. “Front this point onwards” ERP migrations cause age-based data silos. The result? A digital quagmire that makes it difficult for new employees to find their footing and for executives to understand the root causes of inefficiencies.
The Curse of Tribal Knowledge
One of the most significant byproducts of the disorganized Job Folder is the rise of tribal knowledge. This industry-wide phenomenon results in reliance on informal, undocumented knowledge passed down from employee to employee. This culture of “this is how I have always done it” stifles innovation and perpetuates inefficiency. It creates an environment that is anti-data-driven and difficult to scale, as decisions are made based on opinions and traditions rather than data and analysis. Challenging the status quo becomes nearly impossible, as the entrenched practices and resistance to change hinder progress.
The Solution: Industrility’s GenAI-Powered Aftersales Platform
While the current state of the Job Folder might seem bleak, there’s hope on the horizon. Industrility’s aftersales platform offers a solution that can transform this chaos into clarity. By leveraging the power of Generative AI, Industrility can:
- Organize Data: Streamline the organization of all documents and data, making it easier to navigate and find what you need. By scanning these folders and understanding its nature, Industrility carefully prepares the relevant data by sorting and making it ready for internal and external use.
- Enhance Searchability: Implement advanced search capabilities that allow users to quickly locate specific documents or information. By labelling the right data and tagging the documents, manuals, parts lists, Industrility indexes specific metadata so it is easier to find in a few clicks.
- Make Data Asset-Centric: Shift from a document-centric or persona-centric to an asset-centric approach, providing a clear view of each piece of equipment and its associated data. Industrility leverages a unique AI-modeling technique that pivots the data by serial number and model number of the machine equipment.
- Customer-Facing Solution: Industrilty believes “Data silos will continue to exist in our organizations, but our customers should not see them.” Create customer-facing portals that provide easy access to relevant documents and information, and only listing data that is authorized for customers (owners/operators) or distributors (dealers/reps/partners) to see, instead of flooded job folder, creates massive customer satisfaction and increased brand loyalty.
Conclusion
In conclusion, while the dreaded Job Folder represents a significant challenge in the manufacturing industry, solutions like Industrility’s aftersales platform offer a way forward. By embracing these innovative technologies, companies can not only improve internal efficiencies but also provide better aftersales service to their customers, throughout the lifetime of the equipment (often 30-50 years), paving the way for a more organized and productive future.
— Jinesh