- Industrility
- Apps
- Lifecycle
Asset Lifecycle management to Increase Customer Lifetime Value
Asset lifecycle management for the installed base of Industrial Machinery made easy
Installed Base Asset Lifecycle Management (ALM) is a comprehensive strategy for managing the machinery you’ve sold throughout its operational life. By tracking and optimizing every stage, from initial deployment to maintenance, operations, upgrades, and eventual disposal, you can maximize the value of your equipment for your customers, fostering long-term loyalty and repeat business; while enabling the customer to extract maximum value from their assets with maximum uptime.
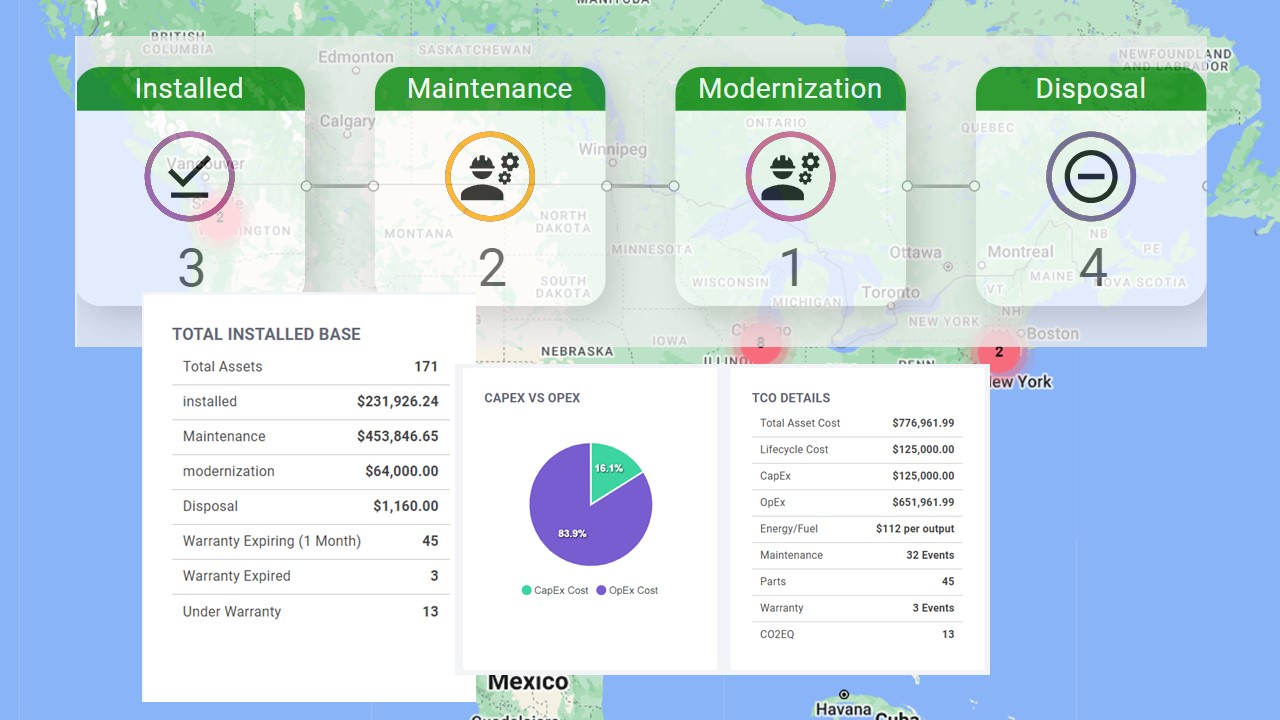
Benefits of Asset Lifecycle Management
- Boost Lifetime Revenue: Extend your revenue stream beyond the initial sale by offering parts, service contracts, upgrades, and resale opportunities through effective ALM.
- Data-Driven Aftermarket: Gain valuable insights into your installed base to optimize aftermarket investments, parts inventory, and service offerings. Empower sales and customer service teams with data-driven tools to increase aftermarket conversions.
- Maximize Equipment Lifespan: ALM helps you extend the life of your machinery by optimizing preventive maintenance schedules, reducing unplanned downtime, and ensuring proper equipment operation.
- Minimize Downtime Risks: ALM proactively identifies potential equipment issues before they escalate, preventing costly downtime and production losses.
- Peak Efficiency & Sustainability: By optimizing equipment performance through ALM, facilities managers can achieve maximum efficiency and contribute to environmental sustainability.
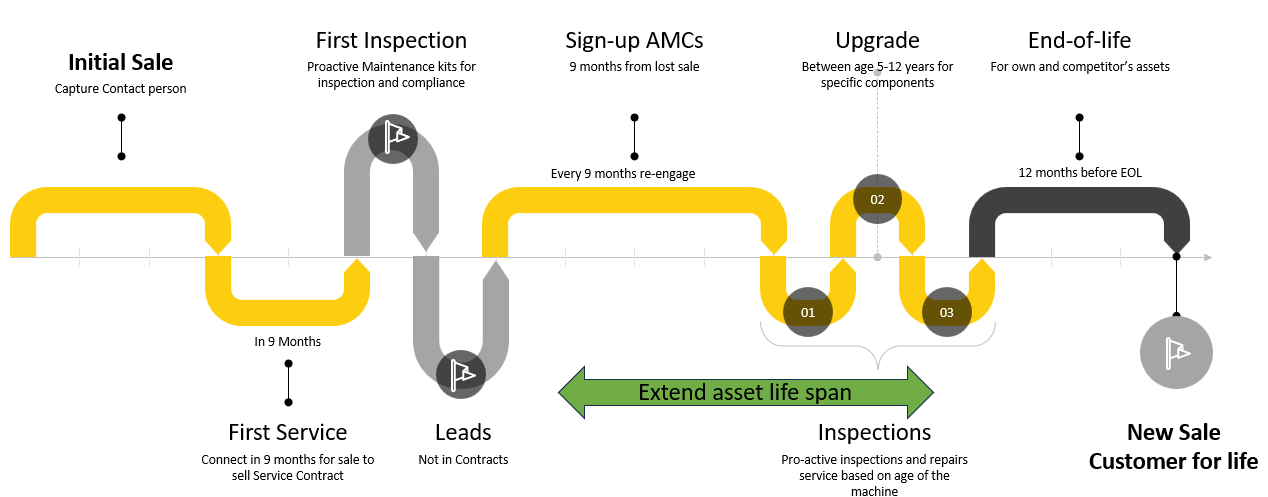
Build a customer for life
Industrility helps manufacturers become more data and AI driven companies
Capabilities
Report accurately on Aftermarket Lifetime Value vs Lifecycle Cost
Aftermarket lifetime value includes the total revenue a manufacturer can expect from their installed product. This is usually calculated by considering product lifetime, lifetime penetration, and average annual parts and service revenue. Collect data about the equipment sale, commissioning service, maintenance contracts, repair, upgrades and retrofits, consumables and energy utilization thereby tracking true total aftermarket entitlement (Internal) and show total lifecycle cost (customer facing). Unlock at least 30% of untapped aftermarket potential by creating visibility.
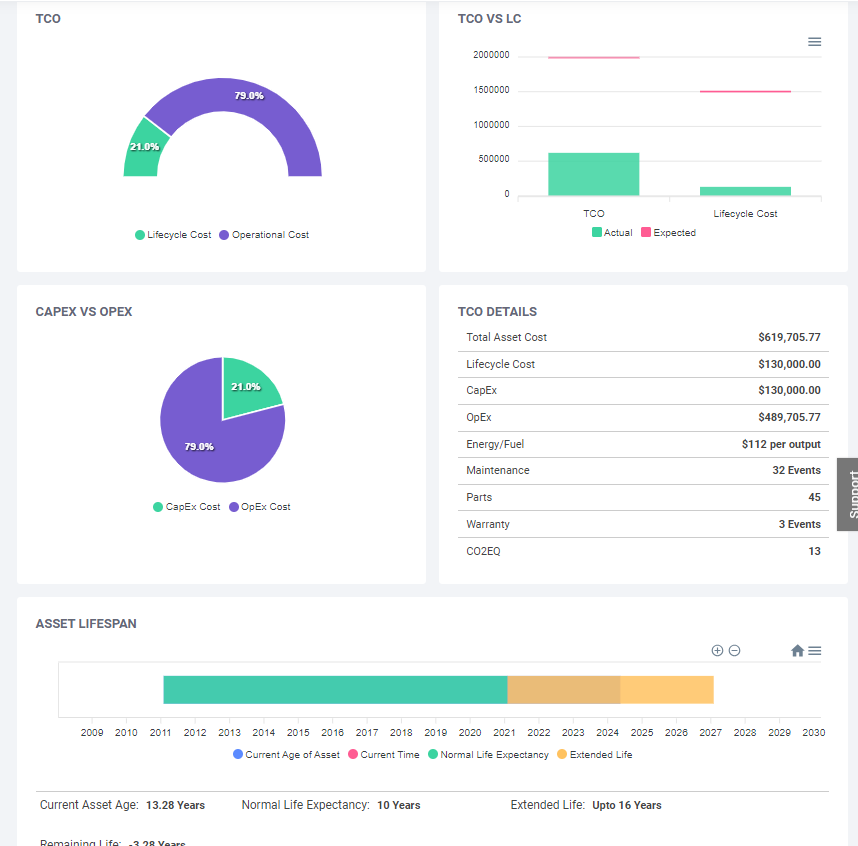
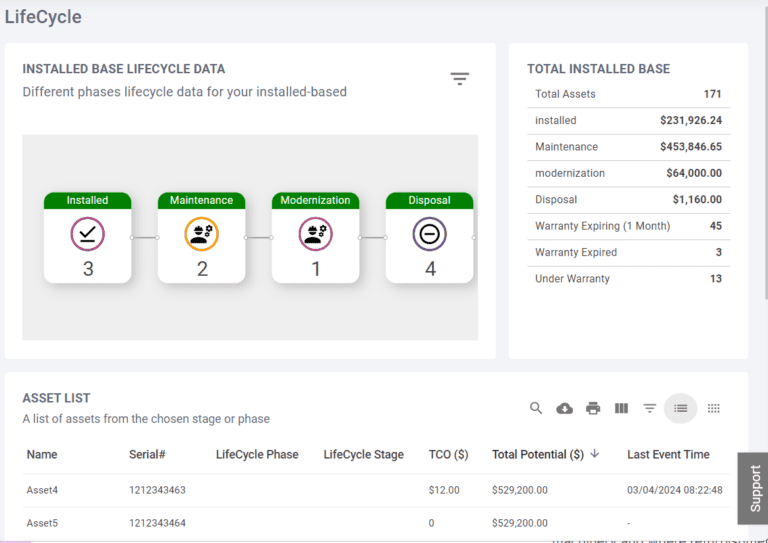
Identify upsell, modernization, service and remanufacturing Opportunities
Enable your sales team with the right data at the right time to improve sales conversion. Preventive maintenance strategies can minimize unplanned downtime, a major contributor to operational costs. Additionally, proactive identification of potential equipment issues, reducing repair costs and extending equipment life. Lifecycle App identifies old machinery and where refurbishment can be implemented. Stay innovative by identifying machinery nearing end-of-life and knowing when to collect, refurbish and sell newer products.Â
Create visibility of life cycle events
Deliver Uptime and efficiency-focused service contracts by creating visibility through every stage of your equipment’s productive life thereby reducing unplanned downtime for your customers, higher equipment efficiency and securing longer-term recurring service contracts with clear customer communication and transparency. Be a partner to your customer in extracting maximum value from your equipment instead of a being a transactional seller.
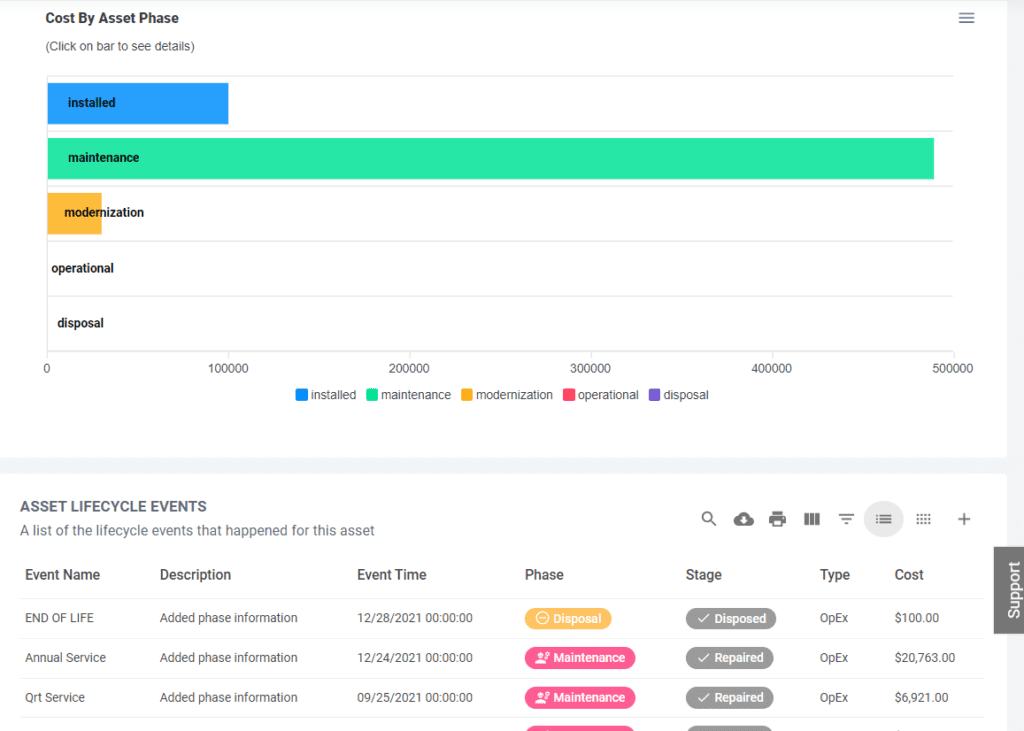
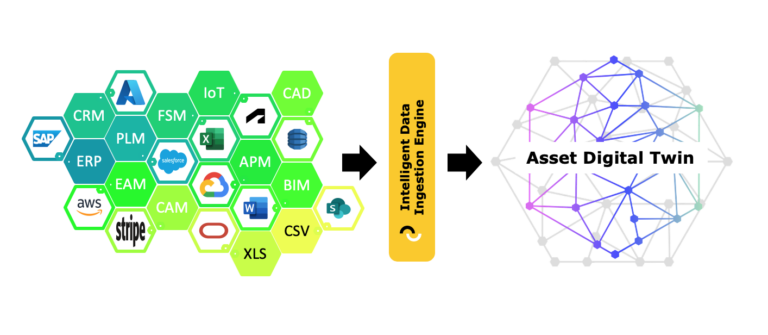
Collect, connect and analyze data for actionable insights
Effortless Data Collection: Simplify ALM by seamlessly collecting data from diverse stakeholders within your organization.
Connect Everything: Integrate data from various systems like ERPs, CRMs, Building Management Systems (BMS), and IoT devices to create a holistic view of your entire installed base.
Actionable Insights: Generate comprehensive dashboards for both your company and your customers. These dashboards provide valuable insights into equipment performance, maintenance needs, and overall asset health.
Built for Industry: Purpose-built for industrial companies, incorporating industry best practices..
Predictive Maintenance Recommendations
Analyze real-time equipment data and integrate with maintenance scheduling software for dynamic adjustments to maintenance schedules, optimizing resource allocation and minimizing downtime.
Monitor planned vs actual revenue
Strategize and budget effectively for total aftermarket value by viewing actual vs forecasted service entitlements.Â
Increasing Asset Lifespan
Ensure efficiency and longevity for your installed base through regular maintenance, condition monitoring, optimized operations, upgrades and retrofits, and asset tracking.
Lifecycle costs vs benefits
Track overall condition of the equipment including TCO calculations, historical maintenance records and consumption for visibility and transparency.
LCC Analysis
Create a customized LCC analysis for specific equipment model, model family or business model for informed purchasing decisions based on long-term value, and not just upfront cost.
Accurate management reporting for service entitlement
Obtain accurate and comprehensive management reporting for service entitlements, helping you effectively manage your service agreements and maximize the value of your installed base and machinery assets.
Take A Look
Isn't It Time For Better Asset Lifecycle Management?
Take A Closer Look At The Powerful And Efficient Lifecycle App
20%
Reduction in downtime resulting in maximum value and reduction in cost
35%
Increase aftermarket entitlement
$$
Increase upsell/cross-sell and remanufacturing opportunities
5+ years
Increased machine lifetime
FAQs
A machinery lifecycle application is a software tool designed to manage the entire lifecycle of machinery assets, from acquisition and installation to operation, maintenance, and disposal. It helps organizations optimize their machinery assets, reduce downtime, and extend asset lifespan.
Key features of Lifecycle include asset tracking and management, maintenance scheduling, condition monitoring, predictive analytics, compliance management, and integration with other systems such as ERP and IoT platforms. These features help organizations streamline their machinery management processes and make informed decisions about their assets.
Lifecycle benefits your organization in several ways, including:
Improved asset reliability and uptime through proactive maintenance and condition monitoring.
Reduced maintenance costs by identifying issues early and preventing breakdowns.
Extended asset lifespan by optimizing operations and implementing upgrades or retrofits at the right time.
Enhanced decision-making through data-driven insights into asset performance and lifecycle costs.
Compliance with regulatory requirements and industry standards through integrated compliance management features.