Part 1: The IoT Revolution in After Sales for Industrial Manufacturers
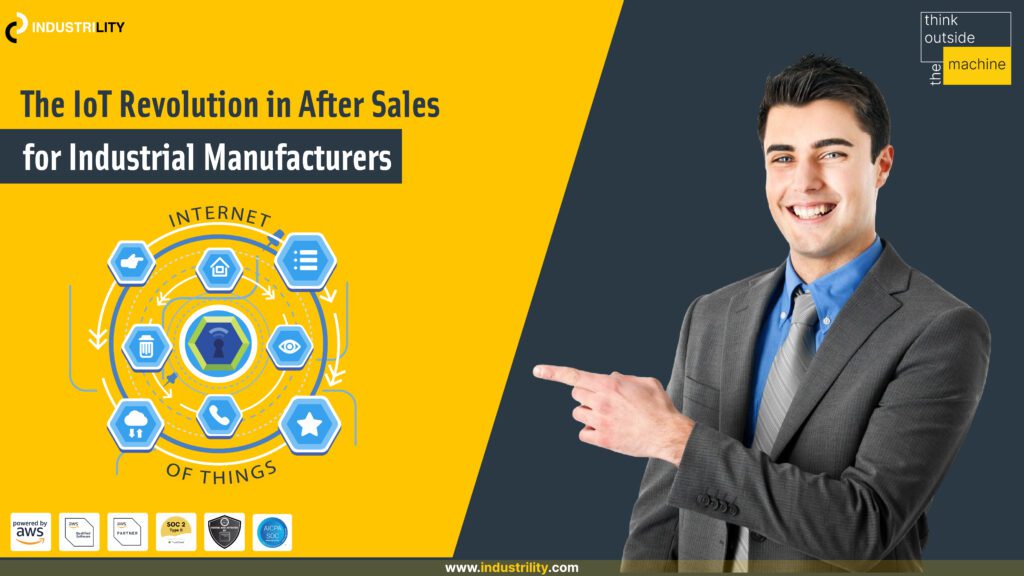
Can you imagine a world where machines could tell you exactly when they’re about to break down—before they actually do? Does that sound like science fiction? Well, it’s not.Â
The IoT revolution has made this possible, transforming aftersales services from a reactive, problem-fixing approach into one that’s proactive and predictive.
Historically, aftersales services waited for problems to arise before responding, leading to costly downtime and repairs. Now, real-time data from connected machines is changing the game. These machines can detect issues early, allowing manufacturers to resolve them before they escalate. The catch? Only 1% of industrial machines are currently connected, leaving a massive gap of 99% and an even bigger opportunity for growth.
What is Industrial IoT?
In simple terms, it’s the process of connecting industrial machines, sensors, and devices to the internet. This connection allows for real-time monitoring, data collection, and control. Technologies like sensors, AI, predictive analytics, and cloud computing all play a major role in making this a reality.
Now, your machines are not just working but talking to you—sharing data that tells you their health, how they’re performing, and even when they might need attention. That’s the essence of IIoT, and it’s revolutionizing the IoT in the manufacturing market.
How IIoT Transforms After Sales?
The impact of IIoT on aftersales is nothing short of revolutionary. By turning reactive services into proactive and predictive, data-driven processes, manufacturers can vastly improve efficiency, cut costs, and keep customers happy. Here’s how:
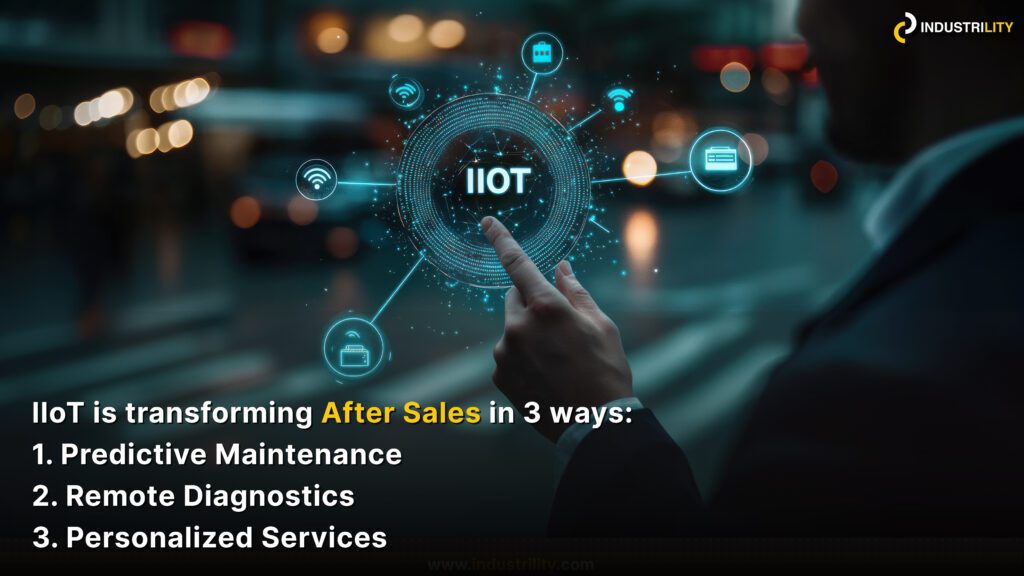
1. Predictive Maintenance
Predictive maintenance uses IoT to monitor equipment health, enabling manufacturers to fix problems before they even occur. According to Deloitte, predictive maintenance powered by IoT can reduce equipment breakdowns by 70% and cut maintenance costs by 25%. Imagine the savings when your machines can self-diagnose, avoiding unplanned downtime.
2. Remote Diagnostics
Gone are the days when a technician had to travel miles just to diagnose a problem. IoT allows for remote diagnostics, speeding up the entire process. This not only cuts costs but also leads to faster problem resolution, making your operations smoother and more efficient by speeding up repair times and reducing operational costs.
3. Personalized Services
With IoT, aftersales services can be tailored to the specific needs of each customer. For example, real-time data from machines can help create personalized maintenance schedules or suggest part replacements based on actual usage patterns. According to HubSpot Research, 93% of customers are more likely to make repeat purchases when companies provide excellent, personalized services. This kind of customization builds customer loyalty, offering a major competitive advantage.
What is the Business Impact of IIoT in After Sales?
The business benefits of IoT are compelling. According to McKinsey, IoT applications in manufacturing could generate an economic impact of $1.2 to $3.7 trillion per year by 2025. That’s a game-changing figure.
Additionally, it’s not just about efficiency as 80% of customers say they’re more likely to continue doing business with a company that offers personalized experiences as per Epsilon. So, by adopting IoT, you’re not just improving your bottom line—you’re improving customer relationships too.
And this is where Industrility is focused on tapping the unconnected machines. We’re building a strategy to increase parts and service revenue digitally, driving manufacturers to automate data collection and sign them up for connected services. By showing the value in these digital upgrades, we can lead customers into accepting the full potential of the IoT.
Conclusion: A New Era for After Sales in Connected Machines
The shift towards connected machines is happening, but it’s still in its infancy. With only 1% of industrial machines connected, there’s a massive opportunity to be explored. By leveraging IoT, manufacturers can transform their aftersales strategies, offering predictive maintenance, remote diagnostics, and personalized services that drive both operational efficiency and customer loyalty.
But here’s the exciting part: the real potential lies in the unconnected machines. With Industrility’s focus on unconnected IoT boilers and other devices, we are building a case for connected machines, unlocking a whole new frontier of efficiency and profitability.
In the next blog, we’ll dig deeper into how IoT can bridge the gap and utilize the untapped potential of these machines, paving the way for an even more efficient and connected future. Stay tuned.
Let’s turn your unconnected machines into powerful, data-driven assets. Connect with us to start your journey toward a smarter, connected future – from identifying untapped opportunities in your installed base to designing a seamless, connected experience that boosts your parts and service revenue, we can help you with everything.
Begin Your Journey of Transformation
I've read enough! I would love to see a demo!
Schedule an 18 min call to discover possibilities