How AI-Powered Aftersales is Revolutionizing CNC Machining
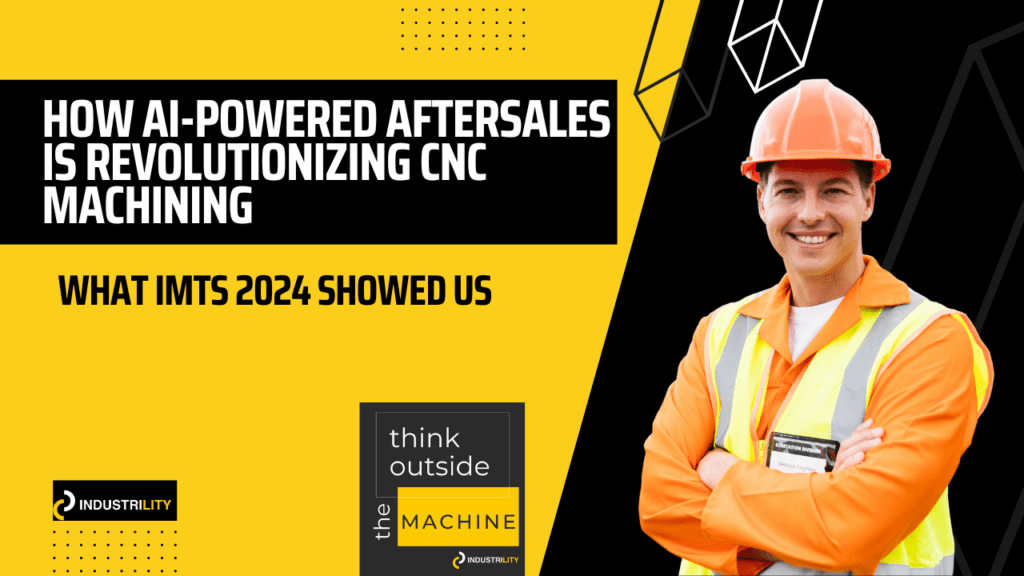
Jinesh Varia, CEO and Founder of Industrility shares his experience of attending the International Manufacturing Technology Show (IMTS) 2024 in this blog post.
As I walked through the vibrant halls of the International Manufacturing Technology Show (IMTS) 2024, I was reminded of how pivotal this event is for the future of the machining industry.Â
Amidst the cutting-edge technology and innovative displays, one theme kept surfacing in my conversations with CNC machining companies—the need for a more efficient, AI-powered parts app that could revolutionize their aftersales strategy and optimize their machining processes.Â
Aftersales support, particularly in CNC machining, is rapidly evolving. Companies are looking for ways to streamline operations, reduce downtime, and improve part identification.Â
AI plays a key role here, unlocking new efficiencies in how CNC machinists interact with their machinery and manage the lifecycle of parts.
1. Finding the Right Machining Tools, Faster and Smarter
Every CNC machinist knows that finding the right machining tool can make or break a job. Whether it’s matching the tool to the material or determining which tools will offer optimal cutting speeds, the traditional method of trial and error is outdated. The need for quick access to the right parts and tools is urgent, and AI can be the catalyst for this transformation.Â
At IMTS, many CNC manufacturers expressed the same frustration: they spend far too much time identifying the correct tools for specific machining tasks. An AI-powered parts app can change this. By leveraging AI, these systems can match machine-specific parameters to available parts, providing machinists with accurate recommendations based on past usage data, material type, and machining goals.Â
Imagine an app that, after inputting your requirements, immediately pulls up the right tooling options for your CNC machine based on historical performance, tool wear, and cutting conditions. AI can predict which tools are the best fit based on machine history, reducing setup time and ensuring jobs are completed faster with fewer errors.
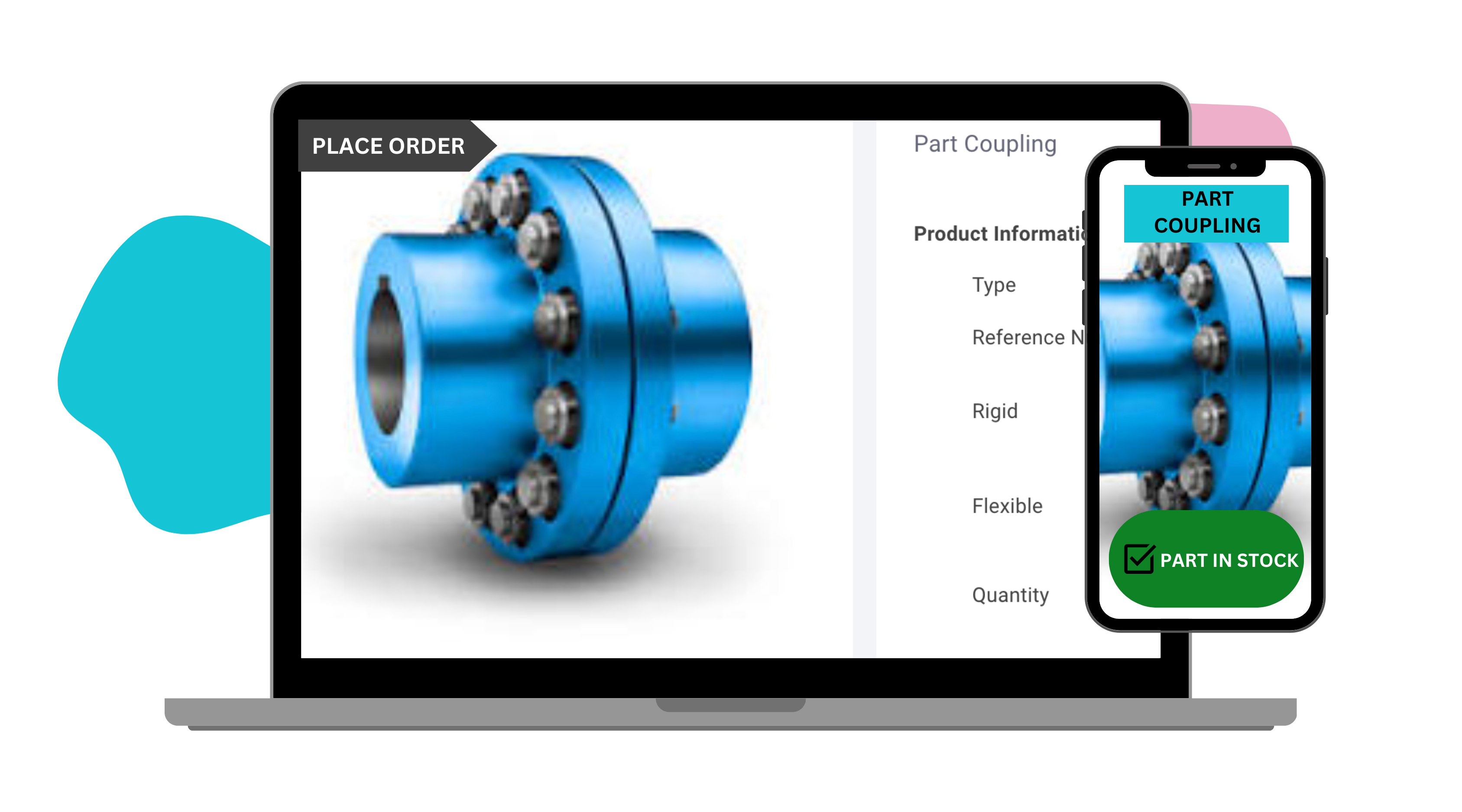
- Bridging CAD to Parts with AI
Another major theme I discussed with CNC companies at IMTS was the gap between CAD design and the actual part production. The journey from design to physical part can be fraught with challenges—wrong materials, incorrect tooling, or even design flaws. AI can seamlessly bridge the CAD to part process, improving accuracy and efficiency.
Through AI-powered aftersales tools, machinists can now take CAD designs and match them directly to available parts, materials, and machining techniques. This ensures that the part produced matches the design intent while minimizing costly errors.
AI can also analyze the CAD files and recommend the most efficient machining strategies, cutting down on time and material waste.
This AI-driven approach to CAD-to-part optimization not only streamlines workflows but also offers a real-time feedback loop. If a part is designed in a way that is difficult or inefficient to machine, the AI can flag this early, saving time and resources in the production process.
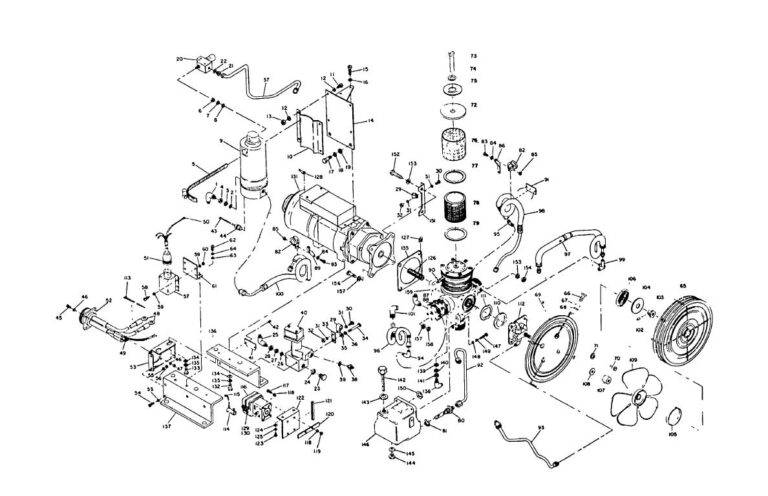
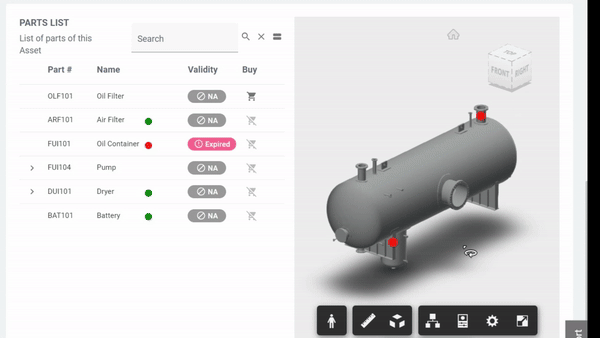
3. Increasing Installed Base Visibility
The installed base—the sum of all parts, tools, and machinery owned by a company—has long been a blind spot for CNC manufacturers. Without visibility into the status and location of every part, companies often suffer from inefficiencies. Parts get lost, the wrong parts are ordered, and machinists waste time searching for what they need.Â
 Â
One of the standout benefits of an AI-powered aftersales app is its ability to provide real-time visibility into the installed base of CNC machines. The app can track the lifecycle of every part, offering insights into when a part was installed, how long it has been in use, and when it will likely need replacement.Â
 Â
At IMTS 2024, several CNC manufacturers shared stories of how a lack of installed base visibility led to machine downtime and lost productivity. By adopting AI-driven systems, CNC companies can access up-to-date information on all parts, tools, and consumables, preventing unnecessary downtime and optimizing overall equipment efficiency (OEE).Â
 Â
Increased visibility also means better predictive maintenance. The AI system can analyze usage patterns and flag parts that are nearing the end of their lifecycle, enabling proactive maintenance before a breakdown occurs. This not only improves uptime but also extends the overall lifespan of the machines.Â
As I left IMTS 2024, it was clear that AI-powered aftersales support isn’t just a nice-to-have—it’s becoming a necessity for CNC machining companies that want to remain competitive. The ability to quickly identify the right machining tools, streamline the CAD to part process, and gain full visibility into their installed base is a game-changer for these companies.Â
At Industrility, we are committed to helping CNC manufacturers unlock the power of AI in their aftersales processes. Our platform provides the tools CNC machinists need to enhance productivity, reduce downtime, and drive operational efficiency—all while ensuring that every part and tool is accounted for.Â
The future of CNC machining is here, and it’s powered by AI. If you’re ready to take the next step, let’s connect and explore how Industrility can help your business succeed.Â
AI AGENTS can be the difference
I've read enough! How Can AI Up My Service Game?
Schedule an 18 min audit call with our founder to understand compatibility