The Future of Machine Uptime: AI-Powered Teammates for Service Technicians
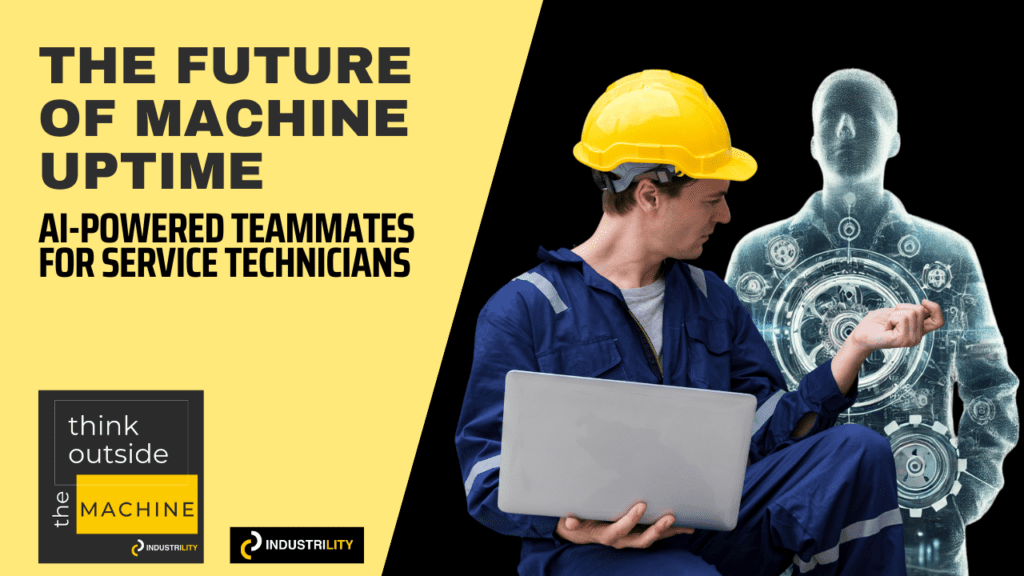
As we embrace the future of industrial operations, one role stands at the heart of operational excellence—the service technician. This unsung hero, responsible for maintaining and ensuring the uptime of machines, often faces a multitude of challenges in installation, maintenance, upgrades, and modernization. However, the rise of generative AI, particularly AI-powered teammate or “smart colleague” or “digital coworker”, is reshaping how service technicians work, making their tasks easier, faster, and more accurate. Let’s dive into how this shift is revolutionizing industrial maintenance.
Empowering Service Technicians with AI Agents
Imagine a technician in the field—time-sensitive repair tasks at hand, working on complex machines, and needing quick access to crucial information. In this scenario, AI-powered teammates can become an invaluable partner, offering real-time assistance through virtual AI agents. These AI agents not only streamline the work process but ensure that the technician is supported every step of the way.
Here’s how AI can assist technicians during key phases of their workflow:
Installation: Smooth, Efficient, and Error-Free
During machine installations, service technicians must navigate a multitude of factors—from understanding intricate configurations to interpreting manuals that might not fully align with the specific machine model. AI agents can analyze and parse operational manuals, guiding technicians step-by-step through installation processes, avoiding potential missteps.
Example: As the technician begins the setup, the AI agent fetches relevant machine configurations proactively (based on both general guidelines and previous installations of the same model or customer industry), ensuring every component is aligned correctly. Using natural language processing (NLP), the AI can even understand queries posed by the technician (e.g., “How do I calibrate the motor on this model?”) and provide instant, context-rich responses
Maintenance: Precision and Proactive Insights
Regular machine maintenance often involves troubleshooting unforeseen issues, which can lead to downtime and additional costs. AI agents can assist by not only referring to standard operational and maintenance manuals but combining this knowledge with historical service records of the specific machine being serviced.
Example: During routine maintenance, an AI agent pulls up past service logs, highlighting a part that has shown signs of wear before, alongside IoT data streaming in real-time (or for that given day) from the machine’s sensors or past service history. Just like the Doctor tests your vitals at every annual physical, AI teammate alerts the technician about the current state of the machine before and after the maintenance to ensure right maintenance was done.
Upgrades and Modernization: Simplified Transitions
Upgrading or modernizing a machine is often a complex task involving new parts, software updates, and ensuring compatibility with existing systems. AI-powered teammates can make this process smoother by cross-referencing parts catalogs with the machine’s specific requirements, ensuring the right components are ordered and used.
Example: The technician needs to replace a module that’s being upgraded to a newer version. The AI agent instantly identifies the required part numbers (or part successors if the part is outdated), checks availability in the inventory, and compares them with the compatibility of the existing machine configuration. Moreover, it can provide detailed guidance on software or firmware updates necessary to integrate the new hardware seamlessly.
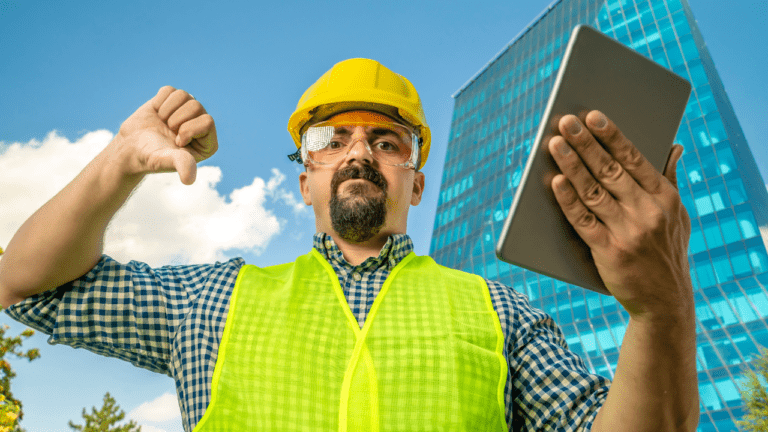
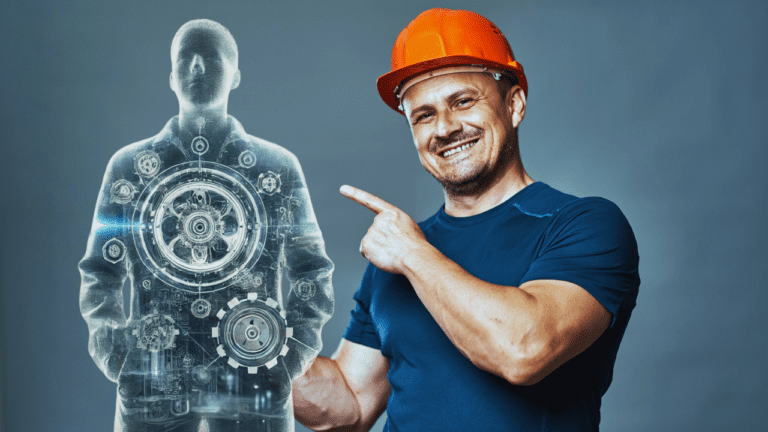
Machine Downtime On Its Way Out
70% of service technicians report improved efficiency thanks to generative AI technologies. These AI-powered tools, acting as smart colleagues, streamline installation, maintenance, and upgrades. This transformation not only boosts work accuracy but also reduces time spent on routine tasks, driving operational excellence in the industrial sector.
AI AGENTS can be the difference
I've read enough! How Can AI Up My Service Game?
Schedule an 18 min audit call with our founder to understand compatibility
Achieving This Vision: Making Manuals and Data RAG-Ready
So, how do we get to this future where every service technician has an AI-powered assistant? The key is ensuring that all the relevant information—general guidance, machine-specific knowledge, real-time sensor data, and parts catalogs—are RAG-ready.
And what is RAG? It stands for Retrieval-augmented generation, a framework that combines information retrieval systems with large language models (LLMs) to improve the accuracy and relevance of the generated text.
In simpler terms, it means the AI doesn’t just make things up; it pulls real info from your IOM manuals, service histories, and sensor data to give the technician super-specific guidance. (Yes, it sounds way too technical, but we promise the AI is the only one doing all the heavy lifting behind the scenes!)
Accelerating this Vision with Industrility
Industrility is at the forefront of bringing this vision to life for manufacturers. By embracing AI-powered solutions and ensuring that all operational data is RAG-ready, we’re not just improving the technician’s experience—we’re transforming the entire maintenance lifecycle of machines.
From reducing machine downtime to enabling technicians to work with more precision and less guesswork, AI-powered teammates represent the future of maintenance, and we are excited to help accelerate that future.
With AI as a constant companion, the technicians of tomorrow will be able to complete tasks faster, reduce costly mistakes, and keep machines running at peak performance. This is the future of machine uptime—driven by AI, powered by Industrility.
— Jinesh